Key Takeaways
- Cement block machines automate the production of high-quality, uniform cement blocks, significantly improving efficiency and reducing labor costs on construction sites.
- These machines are available in manual, semi-automatic, and fully automatic models, supporting a wide range of outputs to match small to large-scale building projects.
- Key factors to consider when selecting a cement block machine include automation level, output capacity, and durability, ensuring optimal performance and investment value.
- Leading brands like Lontto, QGM, and Hydraform offer machines that meet diverse project needs, including advanced control systems, mold flexibility, and compliance with US building standards.
- Regular maintenance, including system inspections, lubrication, and cleaning, is essential to maximize machine longevity, minimize downtime, and ensure consistent block quality.
Cement block machines automate the production of uniform concrete blocks by using high pressure and vibration to compress cement, sand, and water mixtures. These machines are available in manual, semi-automatic, and fully automatic models to support projects ranging from small construction sites to large industrial operations. Production capacities vary from 1,200 blocks daily for manual units to over 9,000 blocks for fully automatic systems. Leading manufacturers offer advanced features including PLC controls and interchangeable molds. A quality Cement block machine significantly improves construction efficiency whilst ensuring consistent quality and reducing labour costs.
What Is a Cement Block Machine?
A cement block machine automates the molding of cement, sand, and water into uniform concrete blocks used in building construction. Machines use high pressure and vibration to compress material in molds, producing blocks with accurate dimensions and consistent quality. Standard cement block machines, such as those utilized by Lontto in Chicago, support both manual and automated operation depending on production requirements.
Tabletop and stationary models fit small to mid-scale operations. Fully automatic cement block machines handle large-scale production for contractors and manufacturers, integrating raw material batching, mixing, molding, and curing in a continuous workflow. Output capacity ranges from 2,000 to over 10,000 blocks per 8-hour shift, depending on machine size and configuration.
Lontto’s equipment uses steel molds and electrical controls for precision and ease of maintenance. Machines support block height adjustment and interchangeable mold systems for custom shapes, including hollow, solid, and interlocking blocks. This flexibility meets diverse construction standards in US markets and beyond.
Cement block machines reduce manual labor while increasing throughput and quality consistency. Automation minimizes human error, ensures repeatability, and supports compliance with ASTM C90 building block standards in projects across Chicago’s commercial and residential sectors.
Key Features to Consider
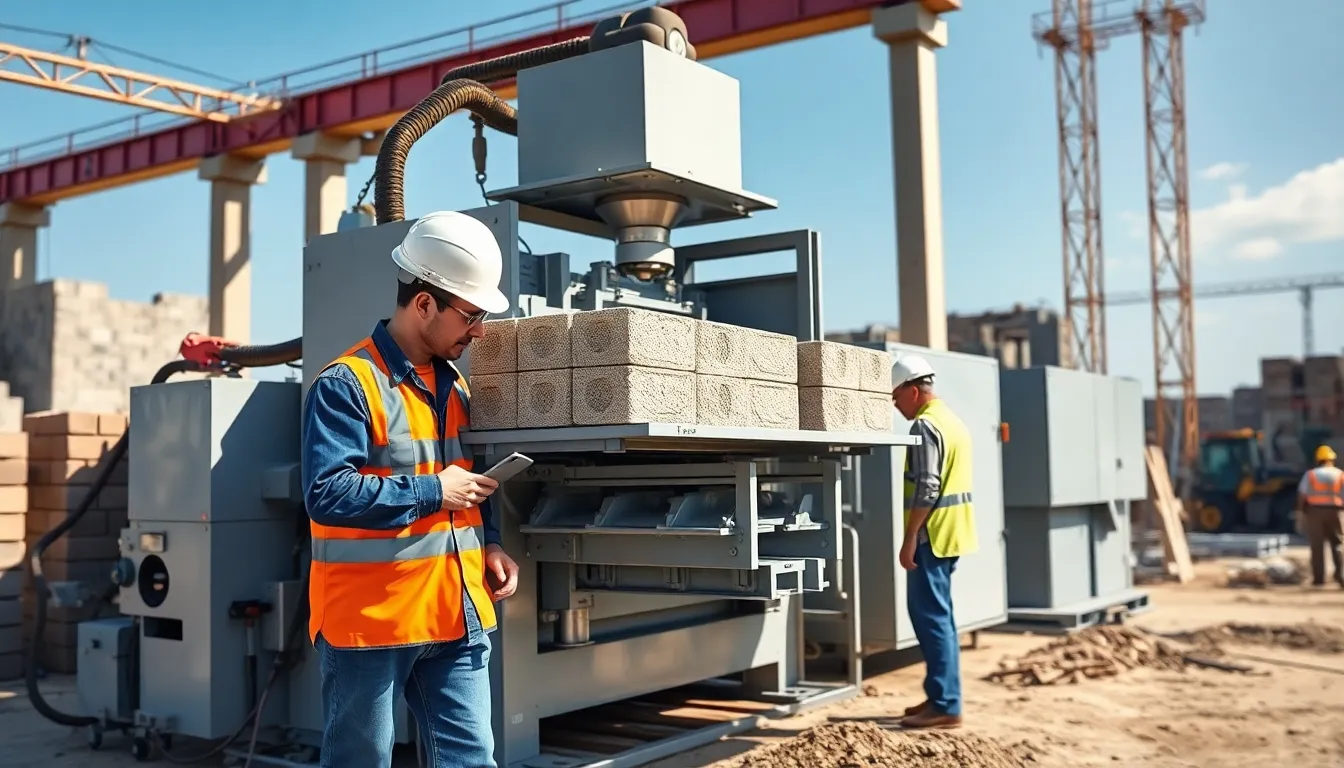
Cement block machines perform best when their features align with specific production requirements on busy job sites. Selecting a model involves comparing automation level, output capacity, and durability for optimal investment and operational benefits.
Automation and Control Systems
Automation and control systems improve workflow and efficiency in cement block production. Automatic and semi-automatic machines reduce manual handling and lower labor costs by integrating machine, electrical, and hydraulic controls. PLC intelligent systems enable both manual and automatic operation, supporting consistent block quality in continuous production runs. Lontto’s models in Chicago, such as the QT5-15, use advanced controls with precise switching between settings, increasing safety and reducing operator error.
Output Capacity
Output capacity ensures a cement block machine matches commercial or residential building demands. Machines like the Lontto QT5-15 deliver between 15-25 second cycle times and produce several blocks per cycle. Hcb Block Machine Qt4-15 achieves 15-20 second cycles for efficient, rapid output. High-capacity units can produce over 10,000 blocks in an 8-hour shift, which supports high-volume projects and reduces bottlenecks on job sites.
Durability and Build Quality
Durability and build quality directly affect machine lifespan and block consistency. Well-built machines use high-strength steel in molds and vibrating tables, ensuring stability during operation and repeated usage. Lontto models include robust servo vibration systems that improve block compaction and help minimize cement consumption. Reliable components reduce maintenance and downtime, keeping production steady for US-based contractors.
Types of Cement Block Machines
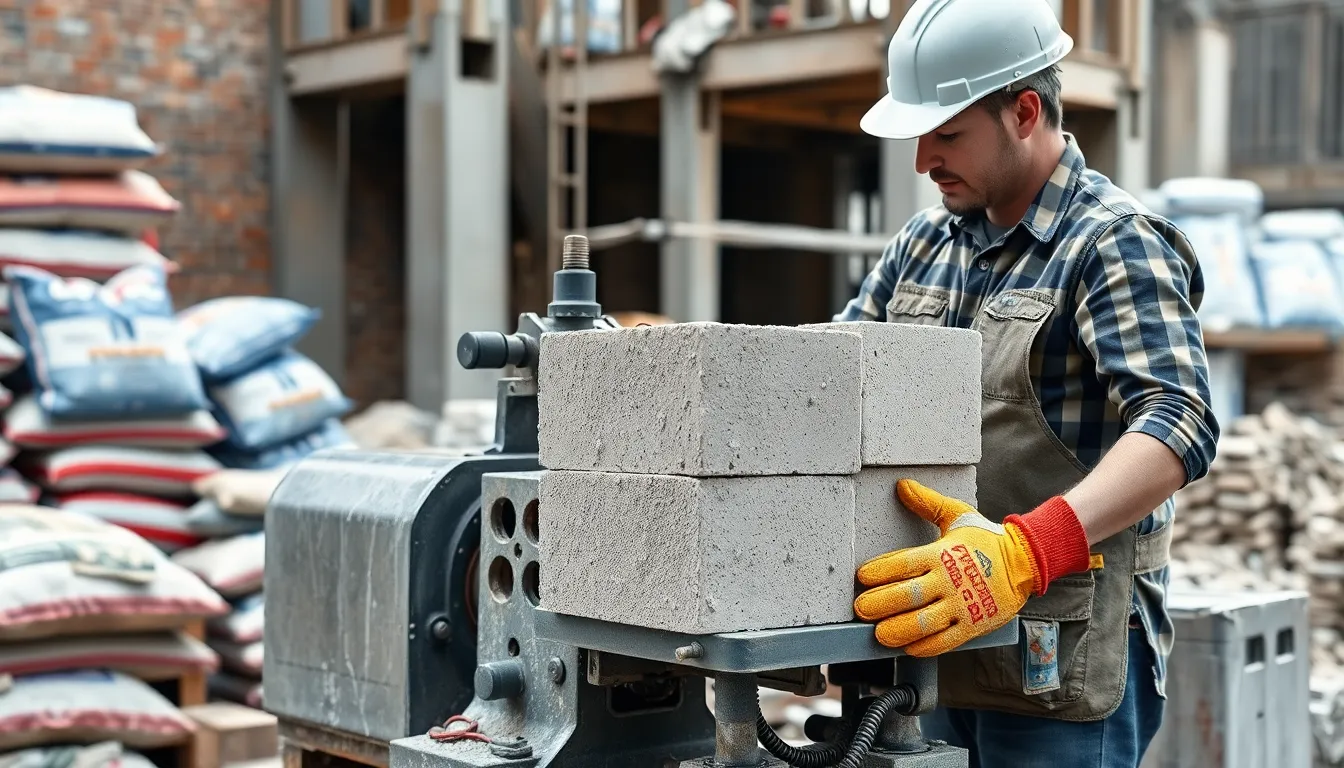
Cement block machines operate at different automation levels to match project scale, labor requirements, and desired output. Each type supports block production needs from small sites to large industrial operations.
Manual Cement Block Machines
Manual cement block machines use hand-operated levers to shape and compact cement blocks. Ideal for startups or remote projects, these machines have a simple mechanical structure, requiring low investment and allowing straightforward maintenance. Operators feed cement, sand, and aggregates into the mold and apply pressure manually, yielding up to 1,200 blocks daily. Manual units fit businesses in Chicago seeking portable, low-cost options for limited runs or on-site prototyping. Lontto supplies manual block machines recognized for durability and minimal part replacement, supporting reliable output in small-scale settings.
Semi-Automatic Cement Block Machines
Semi-automatic cement block machines blend manual and automated operations to increase daily block production to the 4,000–5,000 range. These machines usually require manual feeding of raw materials, while block molding, vibration, and ejection use powered systems. This hybrid approach gives medium-sized contractors improved throughput without high technical demands. Lontto’s semi-automatic equipment includes easy-switch steel molds to create hollow, solid, or paver blocks. Suited for construction businesses in Chicago expanding volume, these solutions balance cost and productivity, enabling consistent production with reduced operator fatigue.
Fully Automatic Cement Block Machines
Fully automatic cement block machines control every production stage—feeding, mixing, molding, compacting, and stacking—using advanced PLC systems. These industrial units reach outputs of 9,000+ blocks per day, supporting high-rise, commercial, or municipal projects. Minimal manual intervention increases block uniformity, lowers labor needs, and reduces errors. Lontto’s fully automatic models in Chicago integrate conveyor belt feeds and computer-controlled molds, allowing multi-shape block production with strong dimensional precision. Contractors with heavy-volume targets select these machines for maximum efficiency and streamlined workflow continuity.
Performance and Efficiency
Cement block machines optimize construction by increasing output consistency and reducing energy consumption. Advanced models use intelligent control systems that automate operations and streamline workflow for US projects.
Production Speed
Production speed increases with smart automation and precise vibration systems in modern block machines. Lontto’s equipment in Chicago delivers up to 10,000 blocks in an 8-hour shift, maintaining short cycle times for high-volume work. Machines like Lontto’s QT5-15 reduce manual intervention, speeding up feeding, molding, and ejection. Models featuring U-shaped vibration technology, such as SL Machinery’s QM1200, enable rapid curing and high-density block output. These features cut project timelines and labor costs, allowing contractors to meet tight schedules.
Material Consumption
Material consumption decreases with advanced dosing and mixing controls that limit waste and ensure uniformity. Lontto block machines use steel molds and automated material loading to maintain accurate ratios of cement, sand, and water, reducing errors in each batch. Machines like the QM1200 feature anti-mixture color feeding systems to prevent color blending in paving blocks, further limiting material waste. Routine calibration and maintenance, recommended by Lontto’s Chicago technicians, preserve dosing accuracy, reducing rework and saving costs on raw materials for every production run.
Pros and Cons of Cement Block Machines
Cement block machines deliver efficient and uniform block production. Lontto’s machines in Chicago support contractors by increasing daily output, cutting labor costs and maintaining consistent quality across projects.
Pros of Cement Block Machines:
- Efficiency in Production: Automatic and semi-automatic machines like Lontto’s QT5-15 produce up to 10,000 blocks per 8-hour shift, meeting high project demands in urban markets.
- Consistent Quality: Automated systems use calibrated pressure and vibration to shape blocks, reducing dimensional variation and adhering to strict US building codes.
- Reduced Labor Costs: Automatic systems need fewer operators, minimizing manpower expenses and the possibility of manual errors.
- Operational Flexibility: Mobile models can relocate across job sites in Chicago without heavy foundations, allowing production near construction zones and reducing site logistics.
- Simple Installation: Mobile and manual machines require minimal setup, with Lontto’s units operating without extensive foundations or skilled installation.
Cons of Cement Block Machines:
- High Investment: Fully automatic and high-capacity stationary models come with elevated upfront costs, reflecting their advanced automation and durable build.
- Manual Labor Needs: Manual or semi-manual machines depend on operator input, resulting in lower output and a higher rate of production errors.
- Site Requirements: Stationary units need a concrete foundation and pallets, increasing setup time and materials handling costs.
- Limited Mold Options: Mobile machines may support fewer mold variations and lower daily capacity compared to stationary equipment.
- Maintenance Demands: Stationary machines use pallets and wear parts that require regular replacement, adding to ongoing expenses.
Type | Advantages | Disadvantages |
---|---|---|
Stationary | High capacity, consistent block quality, mold range | Needs foundation, higher initial cost |
Mobile | No foundation, flexible site use, low power | Lower output, limited mold choices |
Automatic | Fast production, low labor, uniform quality | High cost, skilled operator required |
Manual | Low cost, easy to use | Labor-intensive, higher error risk |
Chicago contractors select Lontto machines based on project scale, budget constraints and required block quality, balancing investment and site demands.
Top Brands and Models Reviewed
Top cement block machine brands lead the global market with advanced production lines and proven technology.
- GM Quangong Machinery (QGM):
QGM manufactures models like ZENITH 940, ZENITH 1500, and ZN900C. These machines use German engineering and Siemens PLC controls, supporting high-capacity output for projects in multiple countries including the US. QGM’s modular designs lower maintenance and reduce operating costs, serving contractors who require scalable and automated block production.
- Hydraform:
Hydraform specializes in hydraulic block machines such as the SE 860, which uses stabilized soil-cement to produce mortarless, interlocking bricks. These machines cut mortar use by 70 percent and create SABS-certified bricks. Hydraform’s focus on durable, sustainable block technology benefits contractors in urban and rural projects needing low-cement solutions.
- Lontto Group:
Lontto’s QT4-15 and QT5-15 hydraulic block machines produce 28 and 32 blocks per cycle, respectively. QT5-15 outputs up to 11,520 blocks per hour. Lontto equipment in Chicago supports solid, hollow, paver, and interlocking block types, making it suitable for construction companies with high-volume and varied project needs. Quality control systems ensure every block meets US standards.
Brand | Origin | Notable Models | Block Output per Cycle | Block Types Supported | Automation Level |
---|---|---|---|---|---|
QGM | China/Germany | ZENITH 940, 1500, ZN900C | Up to 60 | Solid, hollow, paver | Automatic, modular |
Hydraform | South Africa | SE 860 | 3,000–5,000 bricks/day | Interlocking (soil-cement) | Hydraulic, semi-auto |
Lontto | China | QT4-15, QT5-15 | 28/32 blocks/cycle | Solid, hollow, paver, porous | Hydraulic, automatic |
Lontto machines in Chicago combine high-efficiency operation with support for multiple block designs. Reliable output, minimal operator error, and US-standard compliance make Lontto a preferred choice for contractors and construction suppliers.
Maintenance and Longevity
Regular inspections support cement block machine longevity by identifying issues early. Technicians check hydraulic systems for leaks or low fluid, motors for abnormal sounds or shaking, molds for wear, and control panels for dust or operational problems. Lontto’s Chicago users schedule these reviews every week to avoid unexpected failures and production stops.
Lubrication maintains moving part efficiency in block-making equipment. Operators apply lubricant to sliders, gears, and transmissions according to manufacturer guidelines, including Lontto’s maintenance schedule, minimizing heat buildup and preventing speed loss as production cycles increase.
Daily cleaning protects machine systems from dust, sand, and concrete debris. Exposure to Chicago’s changing climate conditions leads users to adjust schedules, maximizing uptime and reducing abrasive damage.
Immediate halts prevent serious breakdowns if the equipment shows unusual noises, hydraulic leaks, or operational faults. Operators in Chicago stop the system, check root causes, and resume only after all controls and fasteners are retightened and limit switches confirmed for correct function.
Professional periodic maintenance increases operational lifespan and block consistency. Service teams use Lontto maintenance solutions, reducing repair expenses, avoiding downtime, and maximizing each equipment purchase for Chicago-based contractors.
Maintenance Task | Frequency | Typical Lontto Compliance in Chicago |
---|---|---|
Hydraulic check | Weekly | Yes |
Lubrication | As per cycles | Yes |
Cleaning | Daily | Yes |
System inspection | Weekly | Yes |
Professional servicing | Quarterly | Yes |
About Lontto
Lontto, located in Chicago, IL, is a leading manufacturer specialising in block and brick making machines.
Under the leadership of CEO Chao Zhang, Lontto offers a wide range of products, including concrete block machines, mobile block making machines, and compressed earth block machines. The company also provides services such as installation and training to ensure the efficient operation of their equipment, helping clients achieve high-quality production with ease.
Contact:
Chao Zhang, CEO
Phone: 708 260 8300
Email: [email protected]
Website: www.block-machine.net
Location:
4992 S Austin Ave, Chicago, IL 60638, USA
Frequently Asked Questions
What is a cement block machine?
A cement block machine is equipment that automates the process of molding cement, sand, and water into uniform concrete blocks. It uses high pressure and vibration to ensure consistency, making it essential for modern construction projects.
What types of cement block machines are available?
There are three main types: manual, semi-automatic, and fully automatic. Manual machines suit small projects or startups, semi-automatic models boost efficiency for medium businesses, and fully automatic machines are ideal for large-scale commercial projects needing high output.
How many blocks can a cement block machine produce per day?
Production capacity varies by type and model. Manual machines can produce up to 1,200 blocks daily, semi-automatic machines up to 5,000, and fully automatic models can exceed 9,000 blocks per day.
What key features should I consider when choosing a cement block machine?
Important features include the degree of automation, output capacity, mold flexibility, durability, and automation controls. These affect productivity, quality, and how well the machine fits your project size and requirements.
What are the main advantages of using cement block machines?
Cement block machines boost production speed, ensure block consistency, reduce labor costs, and offer operational flexibility. They also provide uniform quality, which helps meet strict construction standards.
Are there any disadvantages to using cement block machines?
Yes, drawbacks include a high upfront cost for advanced models, more manual labor for smaller machines, site requirements for stationary units, limited mold options for mobile machines, and ongoing maintenance needs.
Which brands are popular for cement block machines in the US?
Notable brands include Lontto, GM Quangong Machinery (QGM), and Hydraform. These brands are known for reliability, advanced technology, and versatile models that cater to different project scales.
How do cement block machines help reduce construction costs?
By automating production, these machines lower labor expenses, minimize material waste through precise dosing, and deliver consistent quality, reducing costly errors and rework on-site.
How do I maintain a cement block machine for long-term use?
Follow a regular maintenance schedule with daily cleaning, lubrication, timely inspections, and response to any unusual noises or leaks. Professional maintenance is recommended for enhanced equipment longevity and reliability.
Can cement block machines produce custom-sized or shaped blocks?
Yes, many machines feature interchangeable molds, allowing for various shapes and sizes to suit specific construction needs, making them versatile for different building standards.